Resources
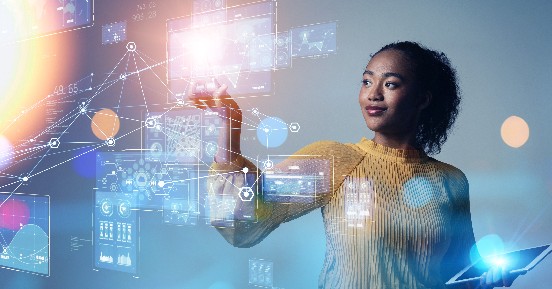
Whitepaper
Iron Mountain's role in the digital transformation value chain
While many solutions are available from the intelligent document processing (IDP) market, organizations must consider scalability, security, integration with third-party software, and the depth of vendor experience. This research brief will explore Iron Mountain's role in the IDP market. Further, we will explore the company's roots in data management and how this deep experience helps it deliver differentiated solutions.
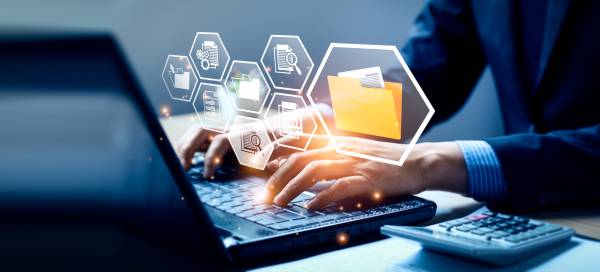
Whitepaper
Boost enterprise-wide innovation with a unified asset strategy
Discover how CxOs and other enterprise decision-makers view innovation, digital transformation, operational excellence, and the value of a unified asset strategy in accelerating their strategic initiatives.